Mastering Industrial Inventory Techniques: A Comprehensive Guide
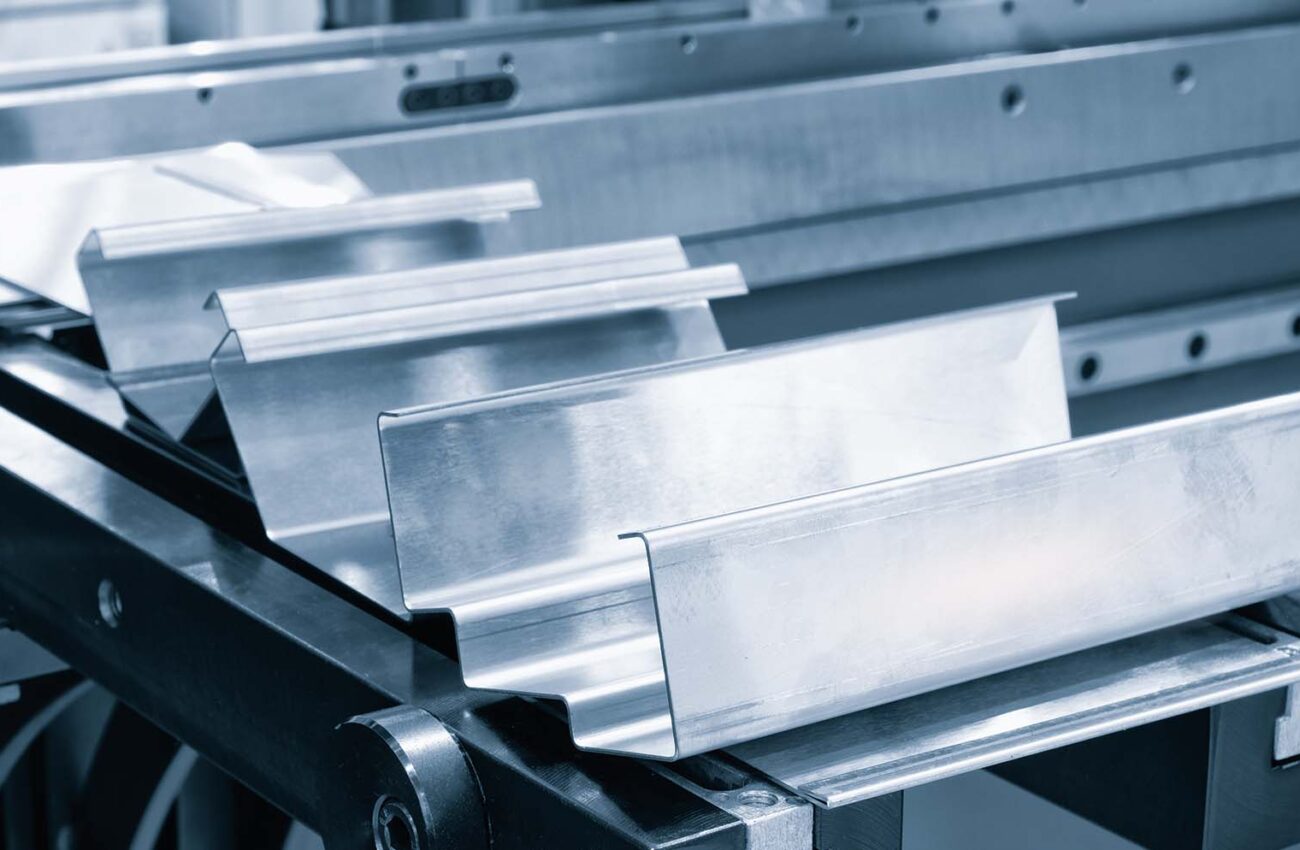
In today’s manufacturing environment, effectively managing industrial inventory is essential for smooth operations and increased profits. This guide explores the key methods and strategies for managing inventory within production facilities. We’ll examine techniques like demand forecasting, safety stock strategies, ABC analysis, and the important role of technology in modern inventory systems. Whether you’re trying to improve existing processes or exploring new approaches, this guide will provide you with the knowledge to manage inventory with precision and confidence.
Decoding Industrial Inventory Techniques
Industrial inventory techniques are systematic methods used to manage inventory efficiently in manufacturing settings. These techniques aim to optimize stock levels, reduce costs, and ensure materials are available when needed, ultimately boosting productivity. Unlike retail inventory, industrial inventory includes raw materials, work-in-progress items, and finished goods. Because of this complexity, a sophisticated inventory management system is needed, tailored to production schedules and supply chain dynamics.
Despite their importance, managing inventory in industrial settings presents challenges like unpredictable demand and supply chain disruptions. Because materials vary – from perishable goods to machinery parts – customized strategies are necessary. To overcome these challenges, companies must use robust inventory management systems, ensuring operational excellence and resilience.
Demand Forecasting: The Cornerstone of Industrial Efficiency
Accurate demand forecasting is vital for effective industrial inventory management. Predicting future needs allows businesses to make informed decisions about purchasing and production schedules, minimizing excess inventory and reducing storage costs. Techniques for demand forecasting range from statistical analysis to expert opinions. Combining these approaches usually provides reliable predictions, helping businesses respond quickly to market changes.
Effective demand forecasting reduces costs, improves stock levels, and enhances customer satisfaction by guaranteeing product availability. By incorporating demand forecasting into their inventory management system, companies can streamline their supply chains and react proactively to market demands, increasing efficiency and competitiveness.
Safety Stock: Guarding Against Uncertainty
Safety stock plays a crucial role in industrial inventory management. It provides a buffer against unexpected demand fluctuations and supply chain disruptions. Maintaining a reserve of inventory allows businesses to handle sudden increases in demand or delays, preventing shortages and protecting their reputation and financial health.
Determining the right safety stock levels involves analyzing sales data, lead times, and service level requirements. Advanced inventory techniques enable organizations to customize safety stock levels to meet operational needs, satisfying customer expectations without overspending resources. Incorporating safety stock strategies into their manufacturing inventory system improves responsiveness and efficiency, giving businesses a competitive advantage.
ABC Analysis: Prioritizing Inventory Efforts
ABC analysis is a key technique for categorizing inventory into three groups – A, B, and C – based on their importance and value. In industrial contexts, it focuses inventory management efforts on the most valuable items, ensuring efficient resource allocation.
Implementing ABC analysis involves evaluating inventory and classifying items by criteria such as annual consumption value. ‘A’ items represent the most valuable inventory, significantly contributing to overall value, while ‘B’ items hold moderate importance, and ‘C’ items are lower-value stock. This classification enables tailored strategies, ensuring strict control over high-value items.
Focusing on ‘A’ items minimizes stockouts and overstock situations, improving cash flow and operational efficiency. ABC analysis empowers businesses to make informed decisions within their manufacturing inventory systems, boosting productivity and profitability.
Choosing Between Just-In-Time and Just-In-Case Strategies
Industrial inventory strategies often involve Just-In-Time (JIT) and Just-In-Case (JIC) approaches. JIT aims to reduce inventory by receiving goods as needed, increasing efficiency and minimizing waste. In contrast, JIC involves maintaining larger inventories to protect against demand fluctuations, ensuring continuous production.
JIT reduces holding costs but requires a reliable supply chain. JIC offers a safety net against uncertainties, though it results in higher holding costs. The choice between JIT and JIC depends on the industry, demand volatility, and supplier reliability. Understanding these needs guides decision-making, helping companies manage inventory effectively.
Harnessing Technology in Inventory Management
Technology is transforming inventory management, offering greater accuracy and efficiency. Advanced systems provide real-time visibility into inventory levels, reducing overstocking risks and improving decision-making.
Tools like RFID tracking, barcode scanning, and cloud-based systems automate data collection and analysis. Leveraging technology within an inventory management system optimizes supply chains and improves operational efficiency.
Future trends, including artificial intelligence and machine learning, promise enhanced demand forecasting. The Internet of Things (IoT) enables sophisticated tracking solutions, creating a connected inventory management ecosystem. By embracing these advancements, organizations position themselves for sustainable growth in a competitive marketplace.